
Our family story
The Griffiths family has been weaving here for over one hundred years. Henry Griffiths bought Melin Tregwynt in 1912 for £760 and then moved there with his young wife Esther.
Their two sons were Benjamin and Howard who left school at 14 to work with his father in the mill. Eluned, his wife, was only 18 when she married Howard and came to live at Tregwynt.
Howard’s son Eifion and his wife Amanda ran the Mill from 1986 up until 2022 when, they set up an Employee Owned Trust. They recognised that the skills and knowledge of all the staff is what keeps the tradition of Welsh weaving alive at Melin Tregwynt, The Trust keeps control of the company safely in the hands of the people who have been a major part of building its success
This photograph was originally taken for the magazine Country Life back in the late 40s.
the mill
see how it's done...

Terry
Terry joined us in 2023. He's the mill manager (a very important role) planning and overseeing the warping, weaving and production of our woollen fabrics here at the mill
Terry brings with him a wealth of experience. See more of his story by clicking the link below.

Paula
Paula's Melin Tregwynt journey story is very special as she is the third generation of her family to work for the bsuiness
Read more about her Melin Tregwynt journey here...

Elsa
Elsa been with us since 2020 and designs and makes teddies, bunnies and hearts (and the occasional dragon) from our fabrics; and she's very good at it.
Read all about her life at the mill here:

Limited-Edition Welsh Wool Collection
Working over the last three years, Melin Tregwynt joined experts and enthusiasts from across our industry for the Gwnaed  Gwlan/Made with Wool project, to re-establish a commercial supply chain for Welsh-grown wool. The outcome is our pilot Welsh wool blanket collection, celebrating three traditional Melin Tregwynt designs, in colourways inspired by our beautiful historic Welsh landscapes.
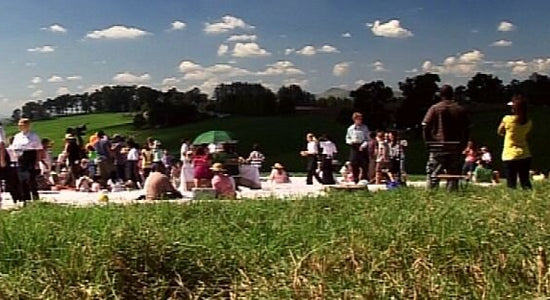
Largest Picnic Blanket in the World
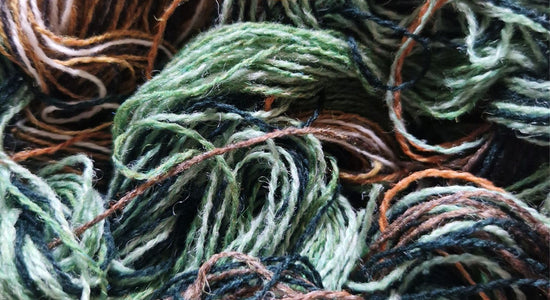
the Adfer recycled wool project
Inspired by a webinar which showcased the creative possibilities of recycled materials and highlighted how brands and manufacturers could integrate these practices into circular business models, we have developed our ‘Adfer’, hand-knit recycled yarn.